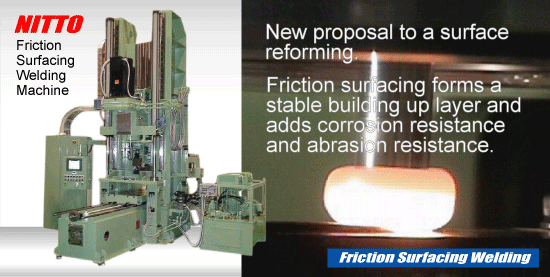 |
|
| Friction Surfacing Welding Machine
|
|
Friction surfacing is a method which
directly builds up softened material to the surface of plate
material with the friction heat. Surface reforming through
friction surfacing forms various kinds of coating layers to
metal surface. For
surface reforming, there are methods such as spray coating,
plasma, PVD and CVD. There are, however, hardly any other
methods but friction surfacing that can form technically
meaningful reforming
layer of 1mm to 2mm thickness.
|
 |
|
 |
|
Theory and features of friction surfacing
 |
Theory is as follows; plate surface is built up by rotating and pushing the surfacing material (round bar) towards the plate and producing friction heat and sliding the plate. Compared to conventional other methods, this is a revolutionary building up technology that has excellent features such as 1)high efficiency, 2)no skill is needed, 3)joining of dissimilar metals is possible.
The process is as follows; when the rotation of the surfacing material ( round bar) reaches the set rotating speed, the base material is brought into contact under pressure, and is moved when the bar material is heated enough. After that, the bar material is crimped plastically with the stable friction heat generated at the boundary surface of rotating bar material and base material, and forms a stable building up layer on base material. Rigid material is used for the surfacing material to improve abrasion resistance. |
|
|
|
|
  |
Theory

 |
Features

 |
|
|
A solid-state process.
|
|
An intense plastic flow makes a fine and homogeneous building up layer.
|
|
Relatively thick layer can be formed and reformed.
|
|
No dilution of the material.
|
|
Automation is easy and no skill is needed.
|
|
It is environmental friendly because neither spatter nor fume is produced.
|
 |
|
|
|
|