|
|
|
|
|
Machine
base

 |
|
Spindle

 |
|
Sliding table

 |
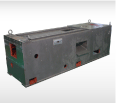 |
To resist high forge force and to have higher welding precision, it has tough welded steel plate construction. It supports high-quality friction welding process with high endurance. |
|
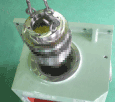 |
The original design of bearing which resists high-speed rotation and high forge force achieves outstanding endurance. The endurance of a spindle cabinet made of cast iron is secured by fixing it to the main body base. (Except for special models such as movable head models) |
|
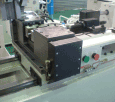 |
By installing a horizontal vise clamp which is lighter than the spindle cabinet on the table, it reduces sliding resistance and achieves a long lifetime. The rail has linear guides and keeps the sliding resistance as low as possible. |
 |
|
|
|
|
|
|
|
Disc brake
 |
|
Spindle drive system

 |
|
Sliding table positioning detection

 |
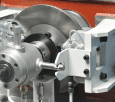 |
To secure stable dimension accuracy, it is equipped with hydraulic disc brake that has high reliability in controlling accuracy. It has an easy structure in changing break pad and makes the maintenance easy. |
|
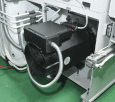 |
The drive of the spindle transmits directly to the material through power belt by the variable motor. The spindle rotation speed can be set at any speed by inverter control. |
|
 |
Installed with high precision magnetic scale, positioning can be detected precisely and also can easily be set by inputting numerically. Neither complicated adjusting nor maintenance is needed with the non-contact high precision magnetic scale. |
 |
|
|
|
|
|
|
|
Chuck unit

 |
|
Clamp unit

 |
|
Hydraulic control

 |
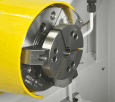 |
The chuck unit on the rotating side can be selected either from 3-jaw power chuck or collet chuck, depending on the shape of the work. The jaw can be designed specially to fit to the
workpiece. |
|
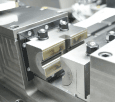 |
The material on the fixed side is clamped by a hydraulic horizontal vise clamp of both sides open-close wick adjustment.
The original structure made high precision and stable grip possible.
|
|
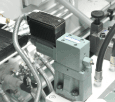 |
In friction welding, control of forge force has a great influence on weld quality. Controlled by originally programmed electromagnetic proportional valve, high-precision welding can be achieved. |
 |
|
|
|
|
|
|
|
Good legibility from central arrangement of pressure gauges

 |
|
Front
Sliding Door


 |
|
|
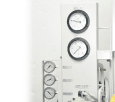 |
By arranging each pressure gauge centrally, high legibility is secured. |
|
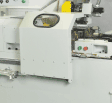 |
It
prevents scattering of swarf and secures the safety
of the operator. |
|
|
|
 |
|
|
|
|
|
|